エコペイズ手数料
<ウェブサイト名>
<現在の時刻>
Jumplinks Jump to content Jump to main navigation Jump to sub navigation Jump to service navigation show menu EN English This page is not available in English. EN English Diese Seite ist auf Deutsch nicht verfügbar. DE Deutsch Esta página no está disponible en español. ES Español 此页面不支持中文。 中文 中文 Esta página não está disponível em português. PT Portugues 日本語ページはございません。 日本 日本 ASK Chemicals Search Main navigation Foundry Cold Box Binder Systems Product Finder Cold Box PU Technology Our Brands ECOCURE BLUE LFSPAC No-Bake Binder Systems Product Finder No-Bake Technology Our Brands INOTEC - Inorganic binder system Product Finder INOTEC Technology INOTEC - technological advantages INOTEC - economic advantages INOTEC - ecological advantages INOBAKE - Inorganic No-Bake Binder Product Finder INOBAKE Technology Coatings Product Finder Coating Technology Our Brands Additives Product Finder Additive Technology Uncoated Castings Lithium free Additives Risers & Sleeves Product Finder Experience Expert Feeding Solution EXACTCAST mini-risers EXACTCAST Riser Sleeves & Auxiliary Products Formulations EXACTCAST riser data for simulation Filters Product Finder EXACTPORE 3D Filters UDICELL Filters EXACTFLO Filters UDICELL Investment Casting Filters Auxiliaries & Release Agents Release Agents Adhesives Cleaners Other Auxiliaries Metallurgy Products Product Finder New Generation of Mold Inoculants Master alloys Cored wire Inoculants Mold Inoculants Pre-conditioners Melt cleaners Design Services Arena-flow® Software From Concept to Design Simulation Services Core Production Expertise & Quality Our Offer Services Success stories Industrial Friction Selector Guide Wear Resistant Friction Resins Refractory Product Advisor Technical Bulletins Success stories Paints & Coatings Product Finder Paints & Coatings Architectural Coatings Can Coatings Wood Coatings Industrial Coatings Protective Coatings Conductive Coatings Additives Fertilizer Coatings General Industrial Latex, textile and special paper applications Carbon Products Resins For Jointing Compounds Toll Manufacturing Innovation Highlights 3D Binder Systems Environment Efficiency & Performance Optimizing costs in use Controlled release fertilizer coating Support Online Academy Live Webinars On Demand Webinars ASK the Expert Ask your question All Questions Casting defect prevention Product usage Environment Profitability Digital Services ASKNow Mobile Download Windows Download ASK Vista Tutorials & Videos White Paper Reduction of VOC emissions New Emission Limits User Manual Professional Articles MAGNASET 2.0 Fluorine-free Riser Filter - Process improvement Release Agents - Correct Classification Filter - Reducing costs in large castings Coatings Saving Potential Sand Binder Systems More Technical Paper Brochures Quality Management Sales Terms & Conditions of Purchase Company History Sustainability Diversity Compliance Quality and environmental certificates News Press releases Shows & Events Career Our Vacancies Your New Employer ASK & ME Our Expert&#039;s Voice Your Start Your Application Contacts Get in touch with us Foundry Chemicals Locations Paint & Coating Industrial Cold Box Binders www.ask-chemicals.com Foundry Cold Box Binder Systems Cold Box PU Technology FundamentalsAs the name already indicates, the PU cold box process is based on the reaction of two components with polyurethane. A polyaddition of the part 1 component, the phenol-formaldehyde resin, and the part 2 component, the isocyanate, is initiated through basic catalysis, usually by means of gassing with a tertiary amine. Performance parameters The hardening reaction is very fast, which makes the PU cold box process attractive for the highly productive production of series components in particular. The high strength level enables fast and automated core production with process reliability. The cores can be cast just a short time after production and feature high thermal stability, which also allows the dimensionally accurate production of water jackets or oil duct cores. Due to their almost pH-neutral properties, high proportions of mechanically or thermally treated used sands from cold box production can be reused.Properties and advantagesRapid model change possible (cold core boxes)Excellent thermal stabilityShort cycle times and high productivity thanks to rapid hardeningSecure core extraction, low core fracture thanks to high initial strengthHigh dimensional accuracySmooth core surfacesLow tooling and energy costsThe main reason why the cold box process is so successful is that it makes it possible to achieve complicated core geometries with high dimensional accuracy and high productivity. When looking at the overall process of core production, the cold box process is distinguished by the fact that the cores that were shot can be mounted to core packages and coated directly after production, i.e. short cycle times are possible from the shot to the core that is ready to use. Excellent disintegration after casting and various possibilities of regeneration with very high reuse rates round off the picture.Fundamentals of the process The components, phenol-formaldehyde resin and isocyanate, are mixed with the mold material, compressed in a core box and hardened with a catalyst. The addition rates can vary depending on the application and mold material; in relation to the mold material, they are usually between 0.4% and 1.2% per part. The binder bridges that develop during the reaction ensure that the molding material compound is stable. After casting, the casting heat has weakened the binder bridges to the extent that the sand can be removed from the cast part by means of mechanical input.Advantages Economic and automatic core production and excellent possibilities for “online production.” The cores are inserted into the ingot or green sand mold as soon as possible after production and then casted. The productivity is about twice as high as that of the Croning method.Requirements for cold box The most important prerequisite for standing one’s ground in the international competition is to produce high quality cast parts with intricate geometry at a reasonable price. The most important market requirements for the PUR cold box resin are:High reactivityReduced emission and odor pollution or a low concentration of monomers (free phenol and free formaldehyde)Reduction of amine consumptionLong processing time (bench life) of the sand mixtureHigh core box cleanlinessHigh strength levelHigh thermal resistance (thermal stability)High stability with respect to water-based coatings (hydro-stability) FoundryIndustrialPaints & CoatingsInnovationSupport CompanyCareerContacts Follow us on: Service navigation Sales Terms & Conditions ASK News Data Protection Disclaimer Imprint & Trademarks © ASK Chemicals 2024
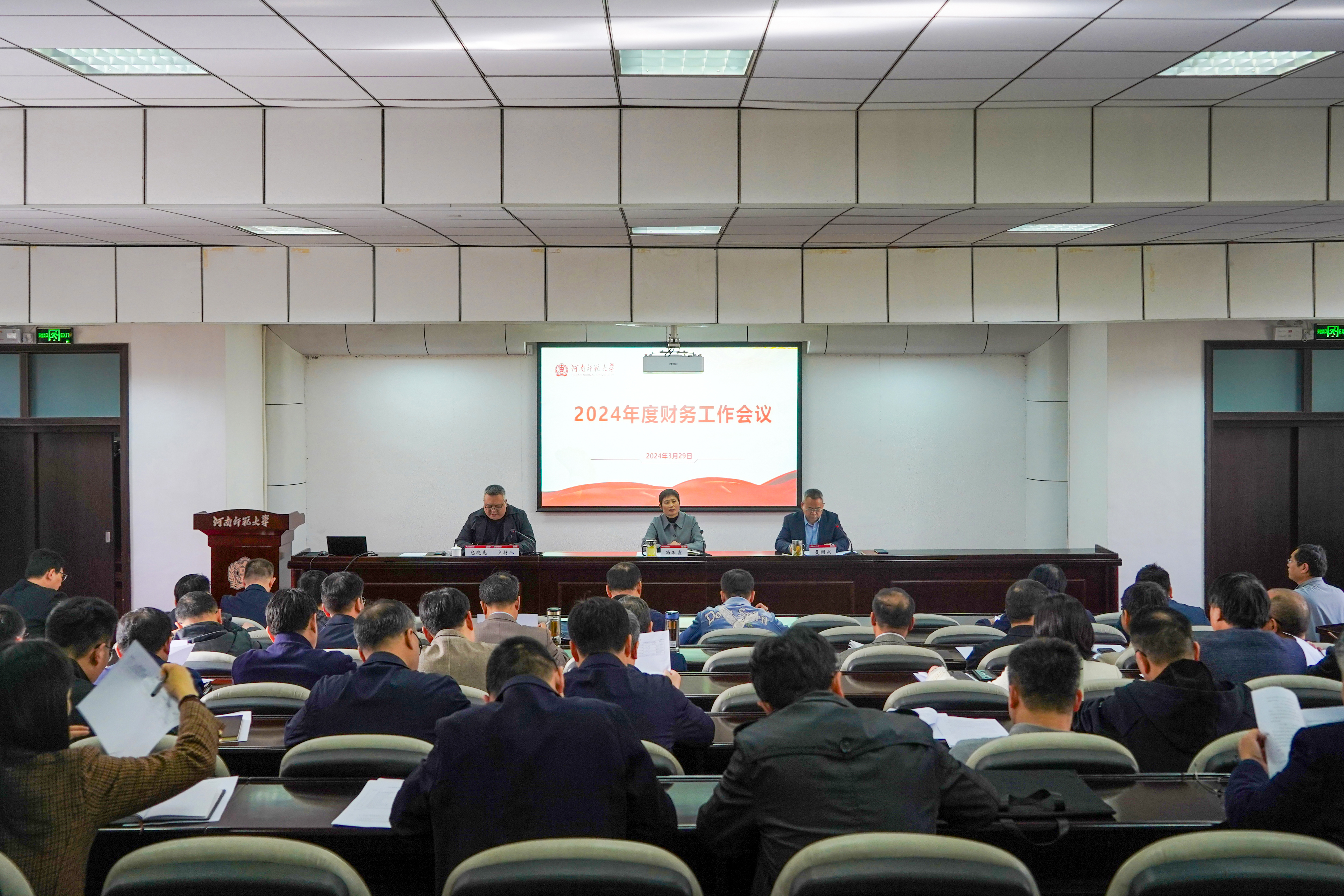